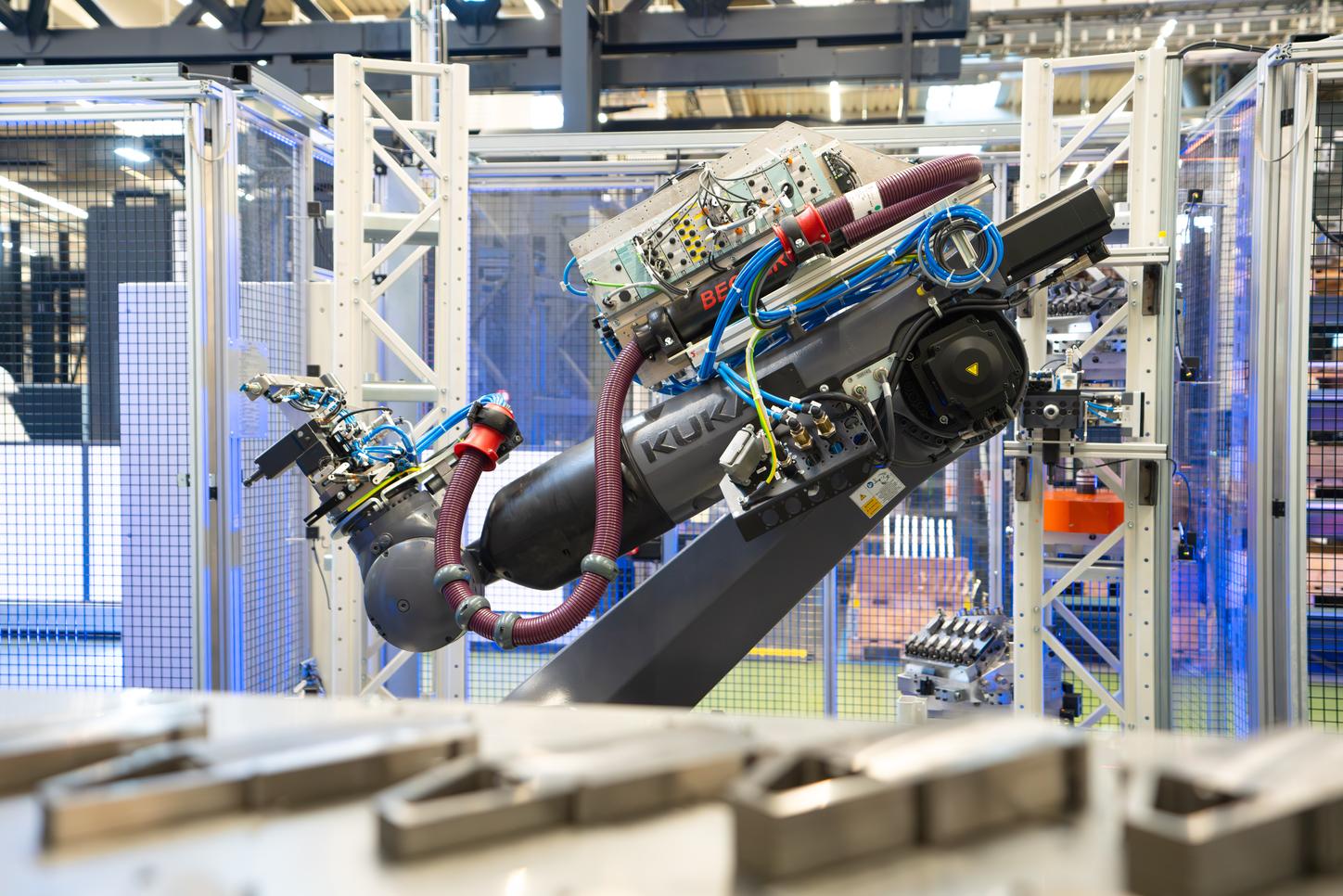
Robo-Hightech für präzise Strahlentherapie
Hauchdünn, aber entscheidend für den Behandlungserfolg
Wolfram ist so hart wie Diamant, so dicht wie Gold und nicht einfach zu bearbeiten. „Doch genau diese Eigenschaften machen es so wertvoll für moderne Strahlentherapie-Systeme“, erklärt Projektleiter und Ingenieur Philipp Mayer. In Kemnath fertigen seine Kolleg*innen und er daraus sogenannte „Leafs“ für die Varian-Strahlentherapiesysteme von Siemens Healthineers.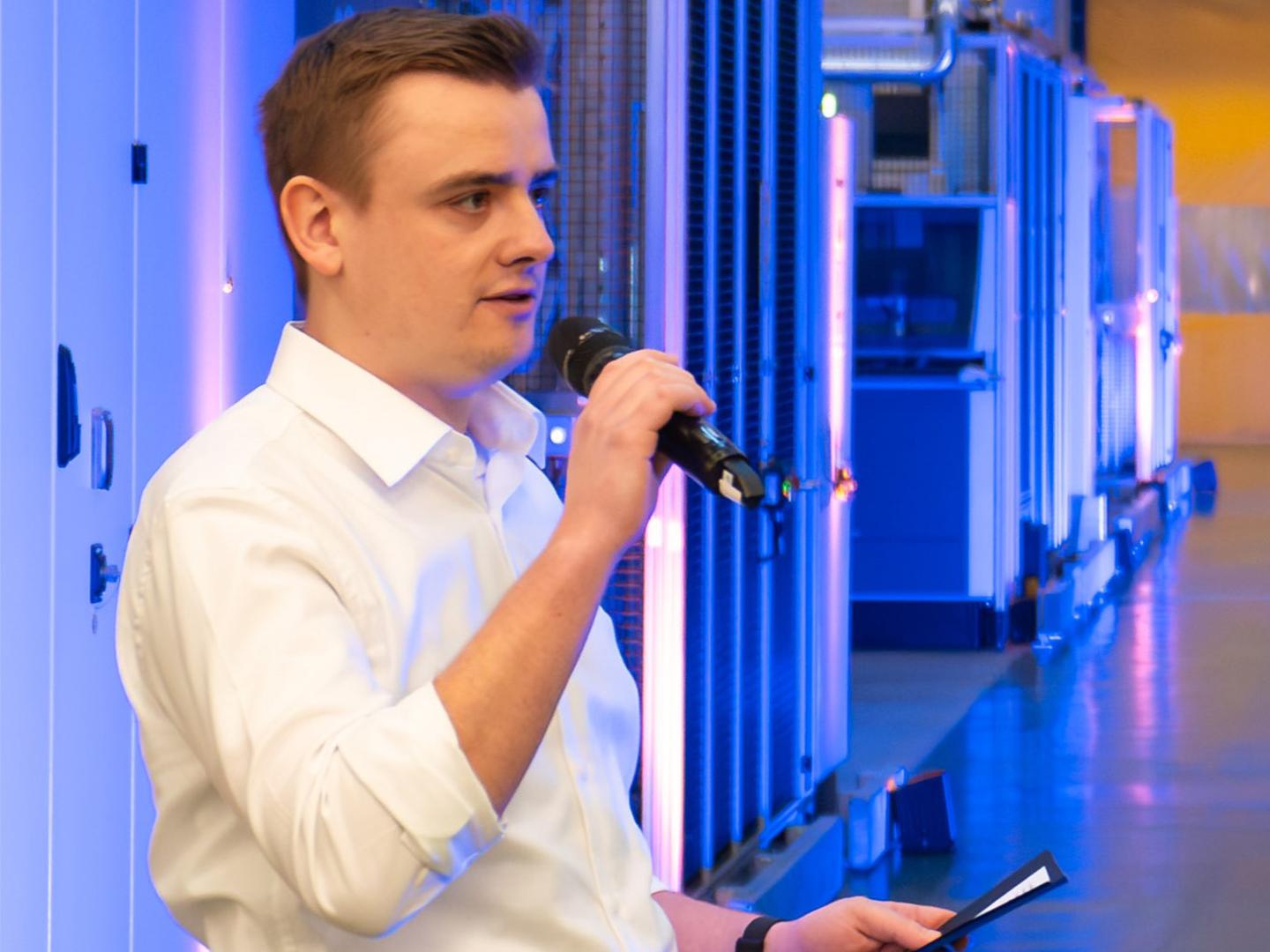
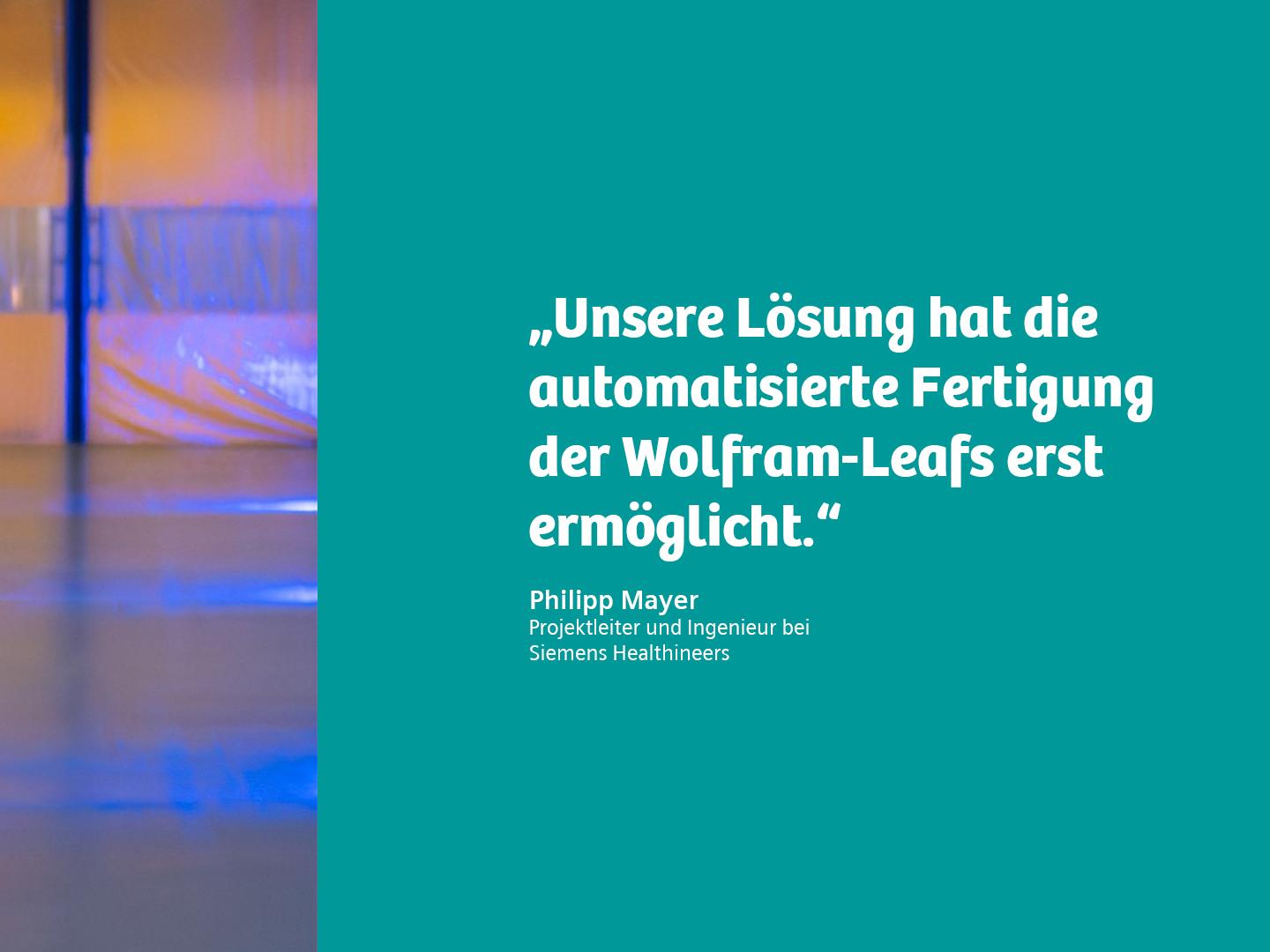
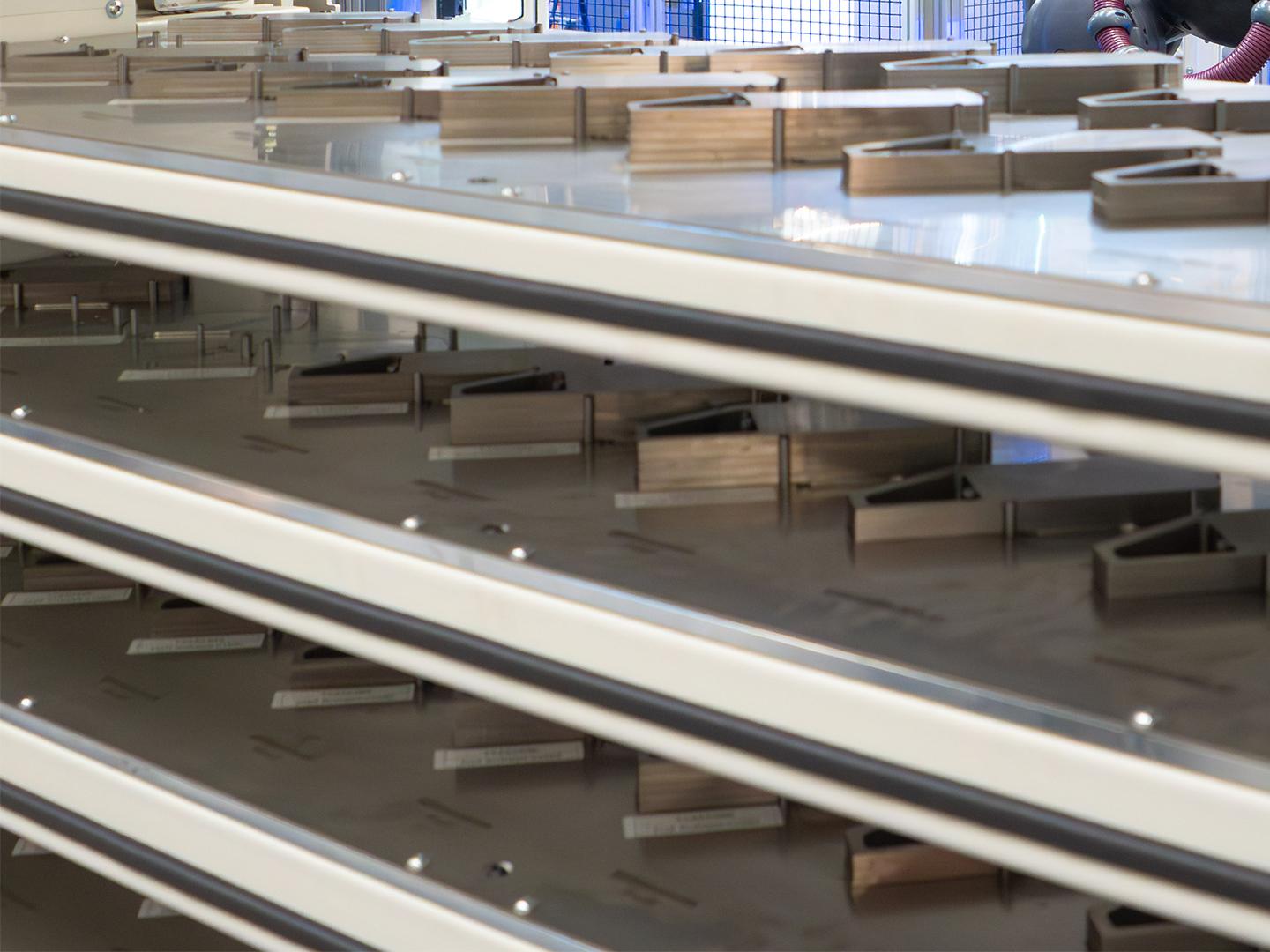
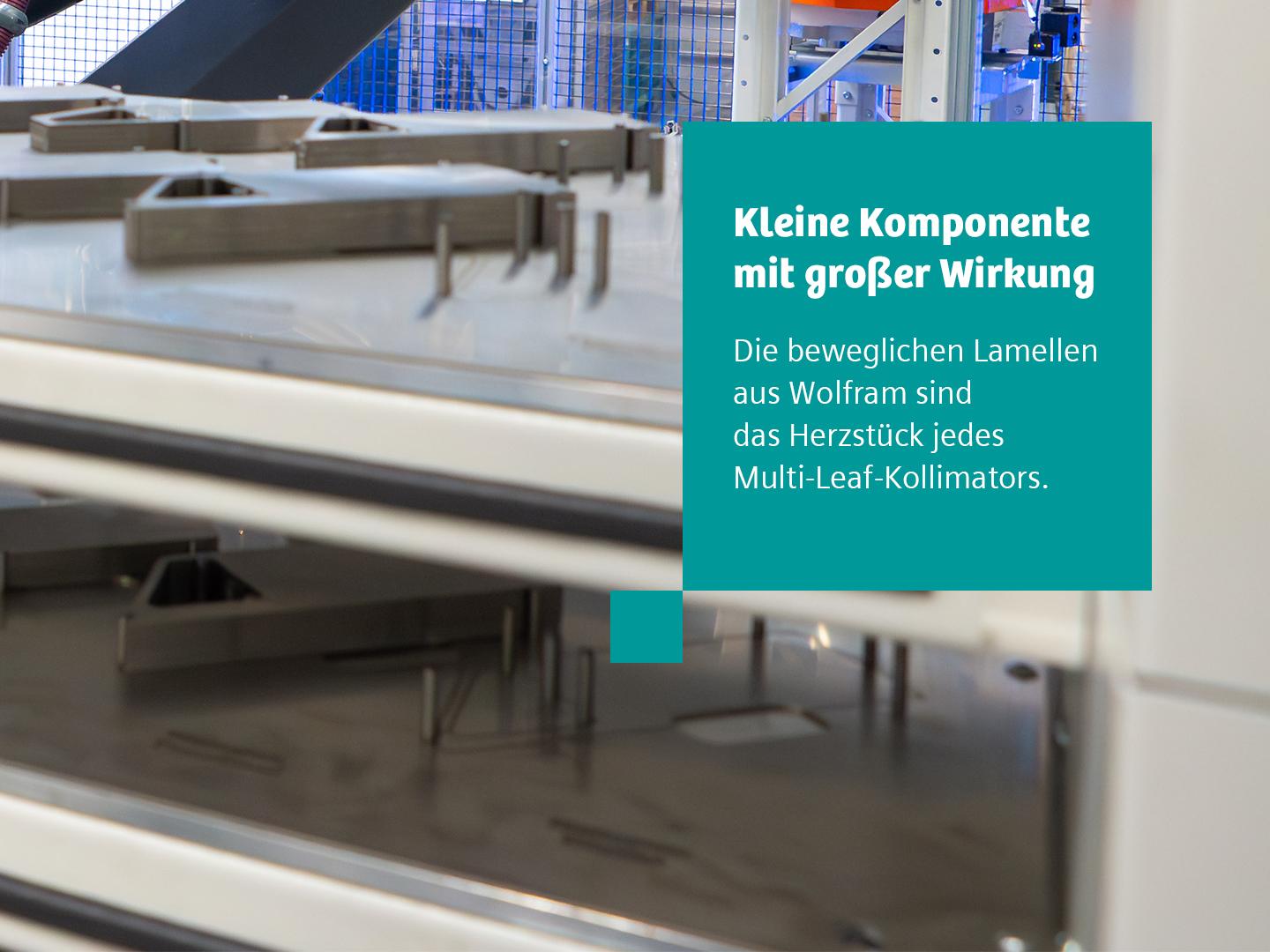
Präzision zur Routine machen
Mit einer neuen automatisierten und digitalisierten Fertigungslinie kann der deutsche Standort diese Schlüsselkomponenten seit Februar 2025 in konstant sehr hoher Qualität und deutlich erhöhtem Produktionsvolumen liefern. Die Anlage verbindet mehrere Fräsmaschinen. Industrieroboter bestücken sie vollautomatisiert.Der Knackpunkt war das Einspannen des Wolfram-Bauteils für den vollautomatisierten Fertigungs- und Handhabungsprozess. Die Lösung brachte eine im Team entwickelte einzigartige und innovative Vorrichtung. Für den jungen Projektleiter steht fest: „Unsere Lösung hat die automatisierte Fertigung der Wolfram-Leafs erst ermöglicht.“
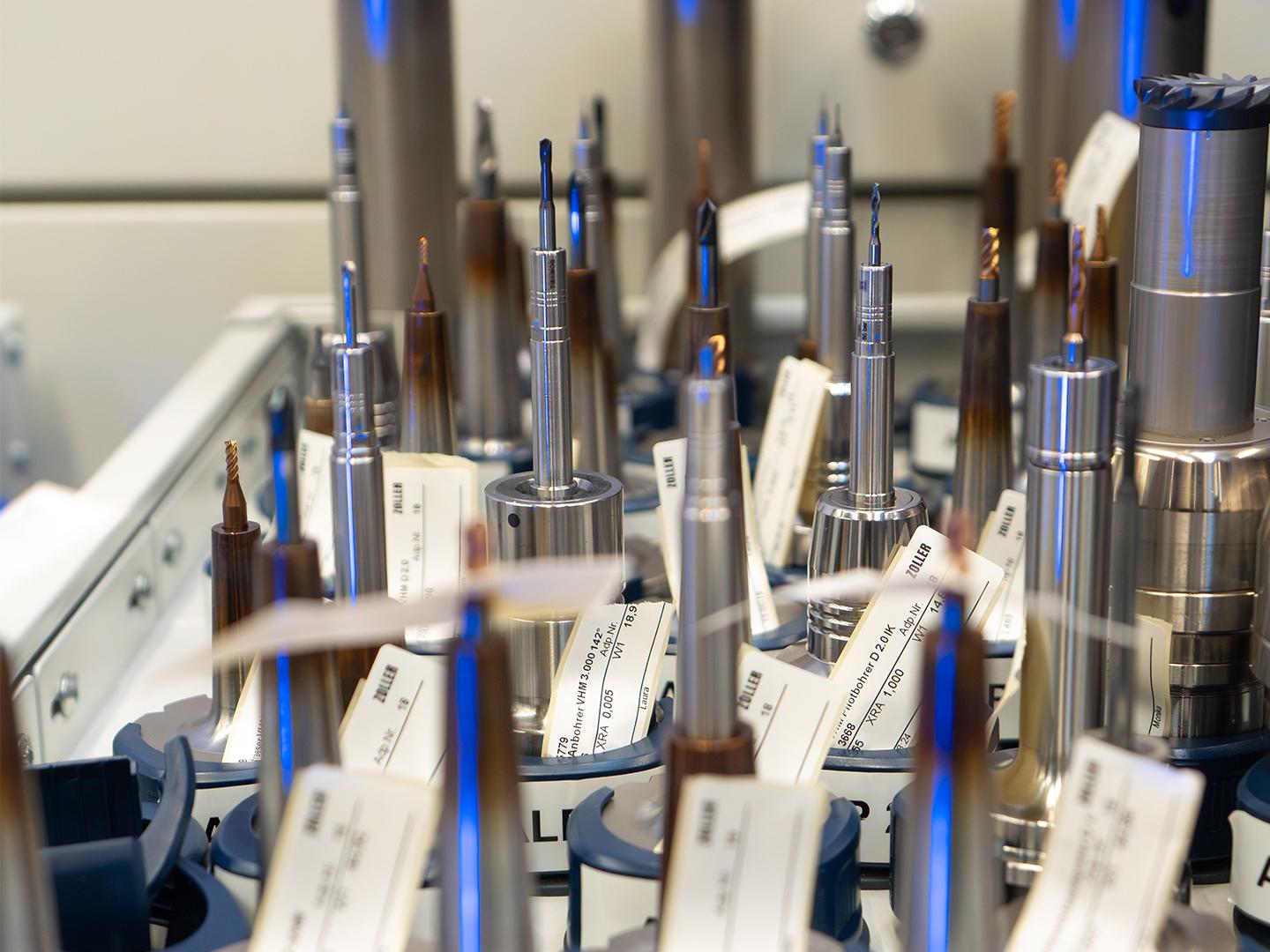
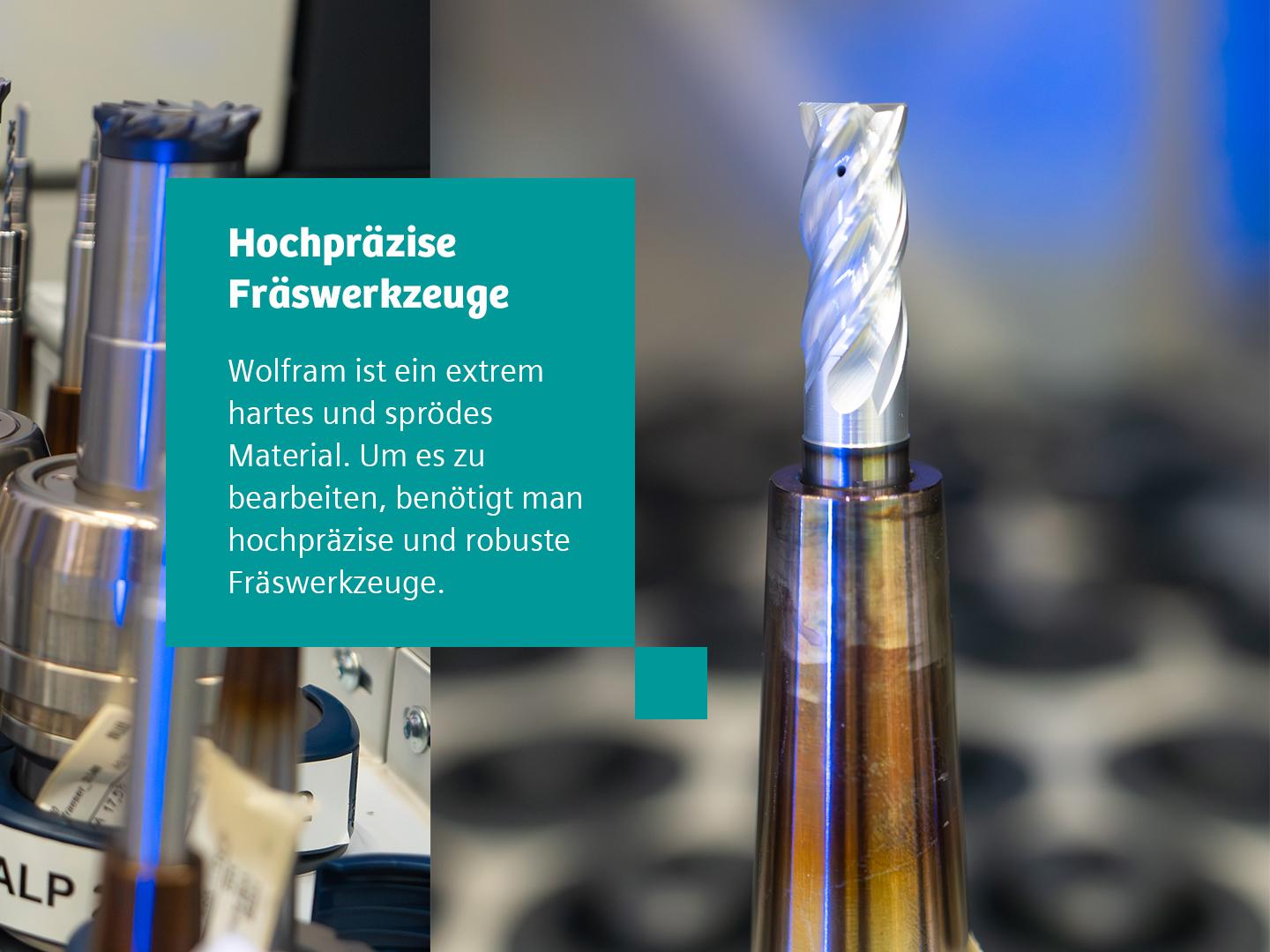
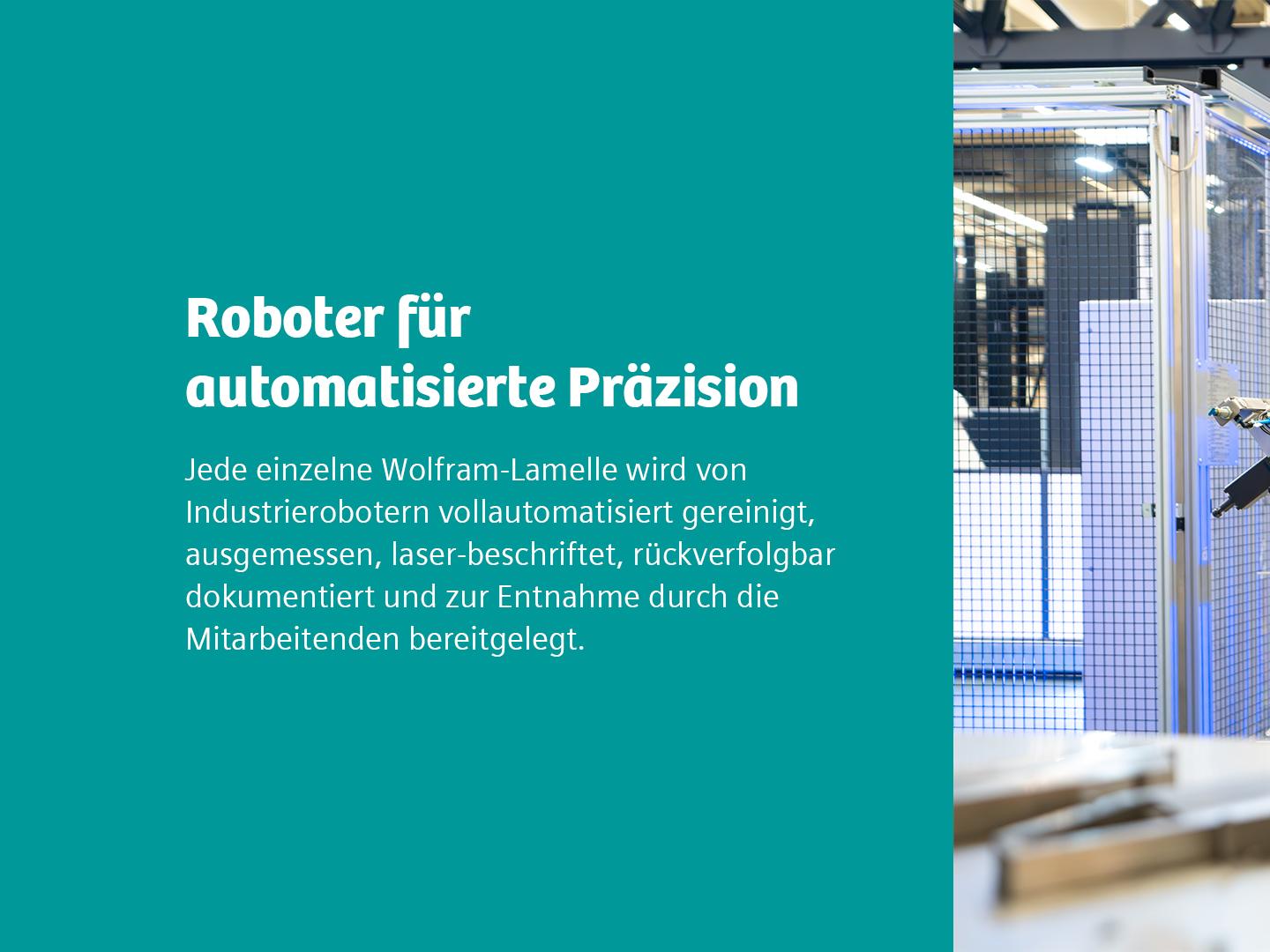
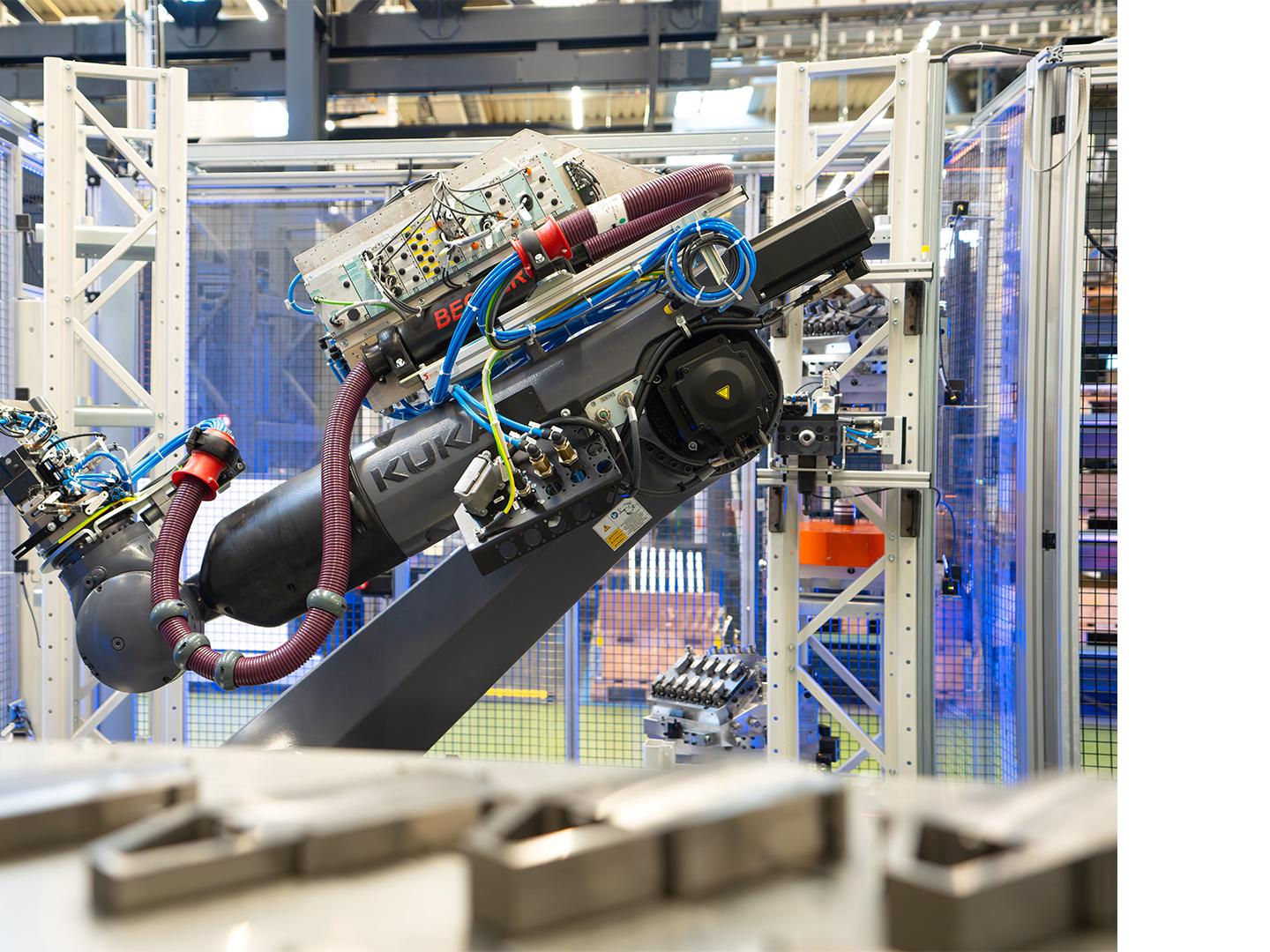
Die Automatisierung erhöht die Fertigungstiefe unseres Standortes. Das heißt, wir haben den Produktionsprozess nun zu großen Teilen selbst in der Hand. Das ermöglicht wiederum eine gewisse Unabhängigkeit unseres Unternehmens von externen Lieferanten, eine besonders zuverlässige Versorgung unserer Partner und langfristige Lieferplanungen. Und das sogar dann, wenn wir von einem weltweit wachsenden Bedarf an Hochpräzisionskollimatoren ausgehen.
Rainer Häupl, Leiter des Mechanik Center Kemnath