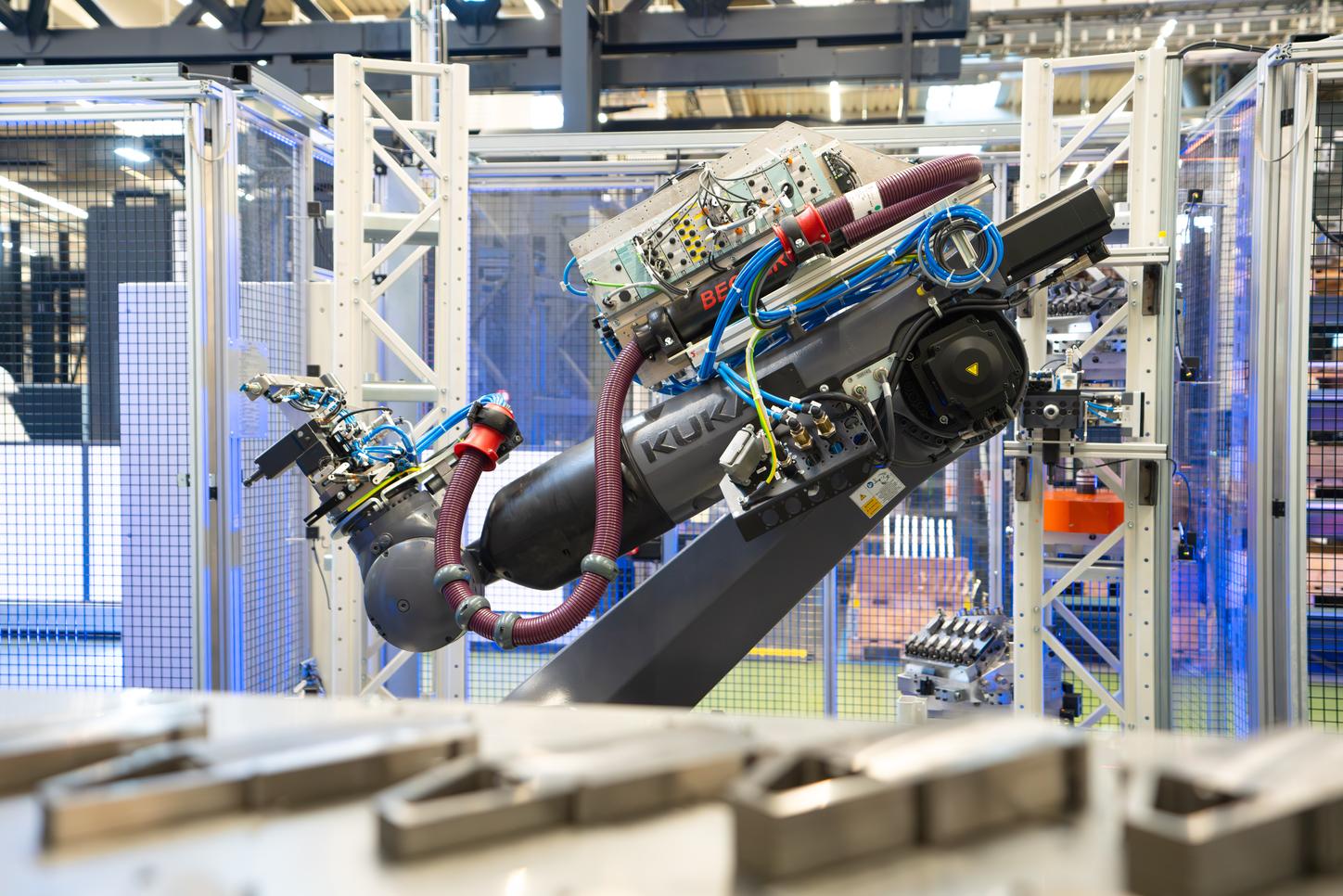
Robotic precision for advanced radiotherapy
Ultra-thin – yet mission-critical
Tungsten is as hard as diamond, as dense as gold, and not easy to work with. “But those same properties make it invaluable for modern radiotherapy,” explains project lead and engineer Philipp Mayer. At the Kemnath site, Mayer and his team use tungsten to manufacture what are known as “leafs” – used in the Varian radiotherapy systems of Siemens Healthineers.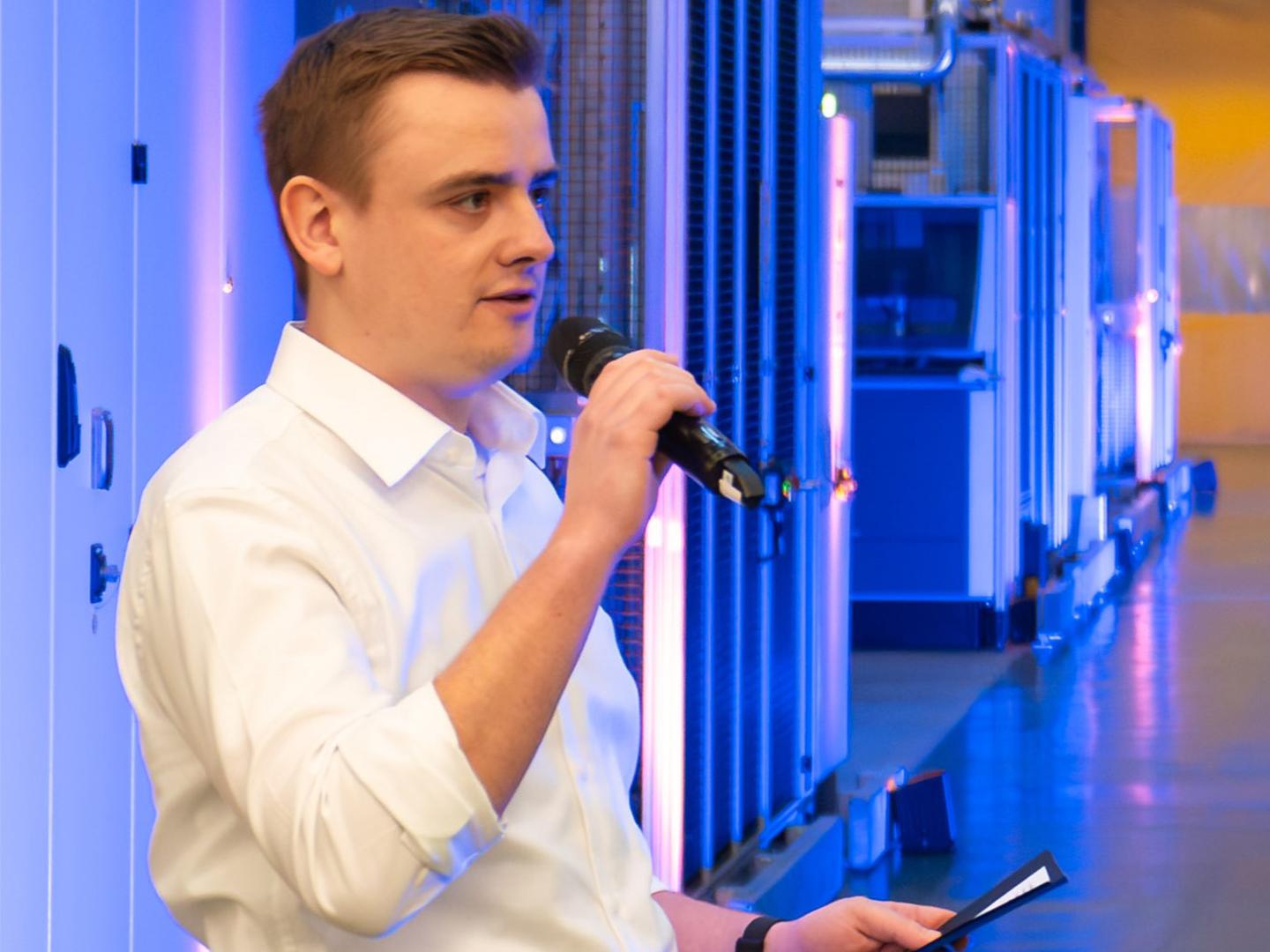
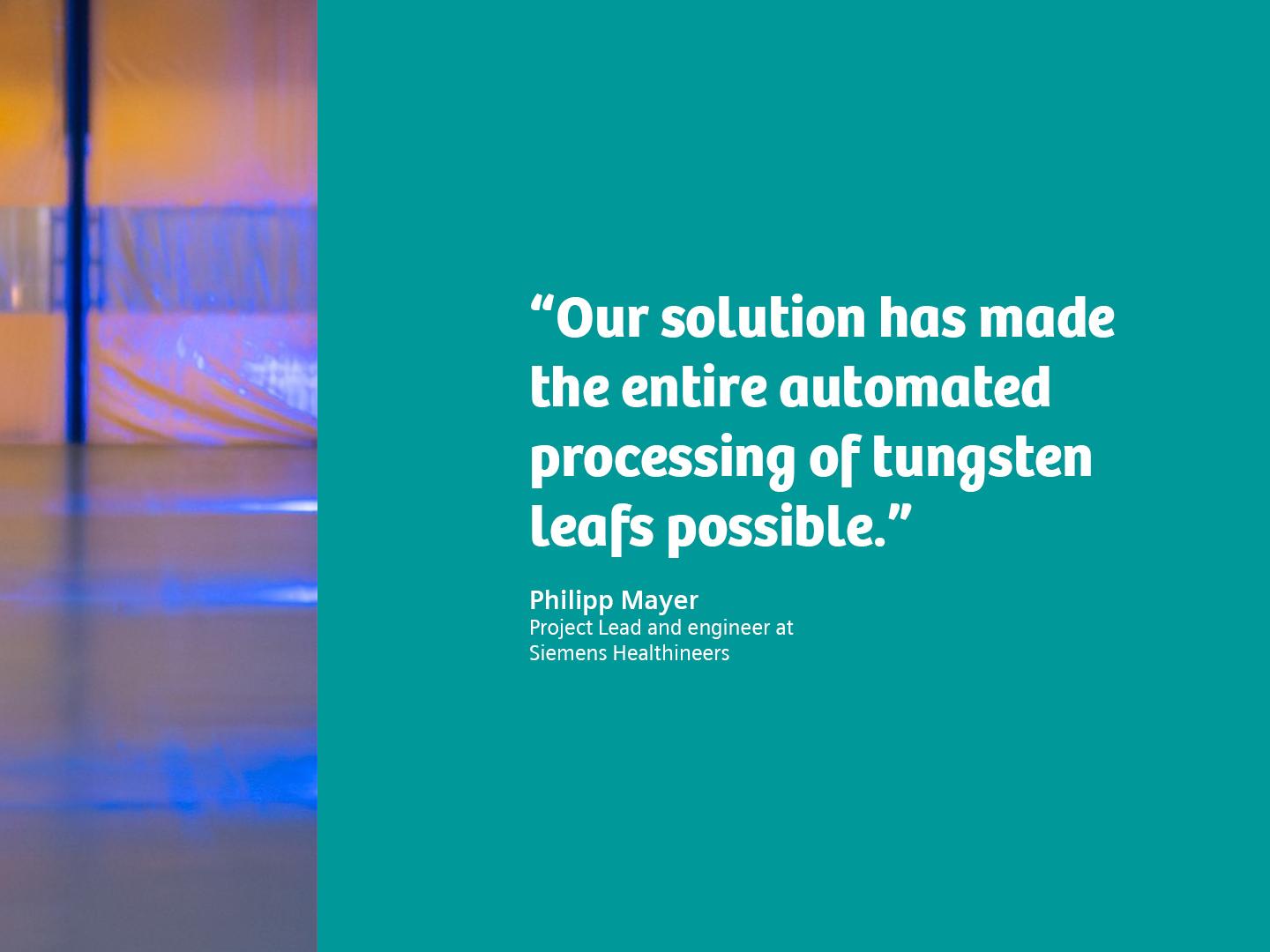
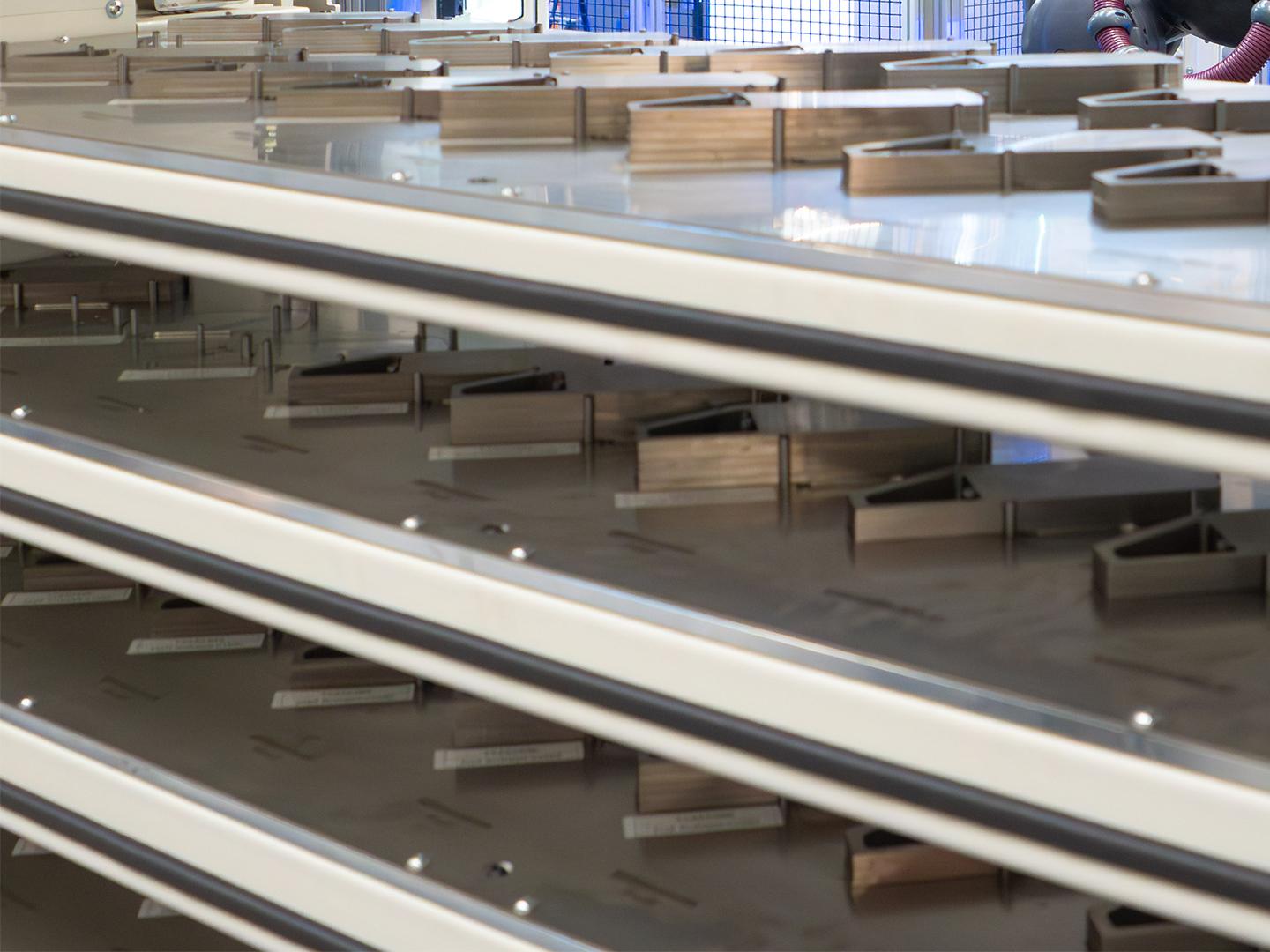
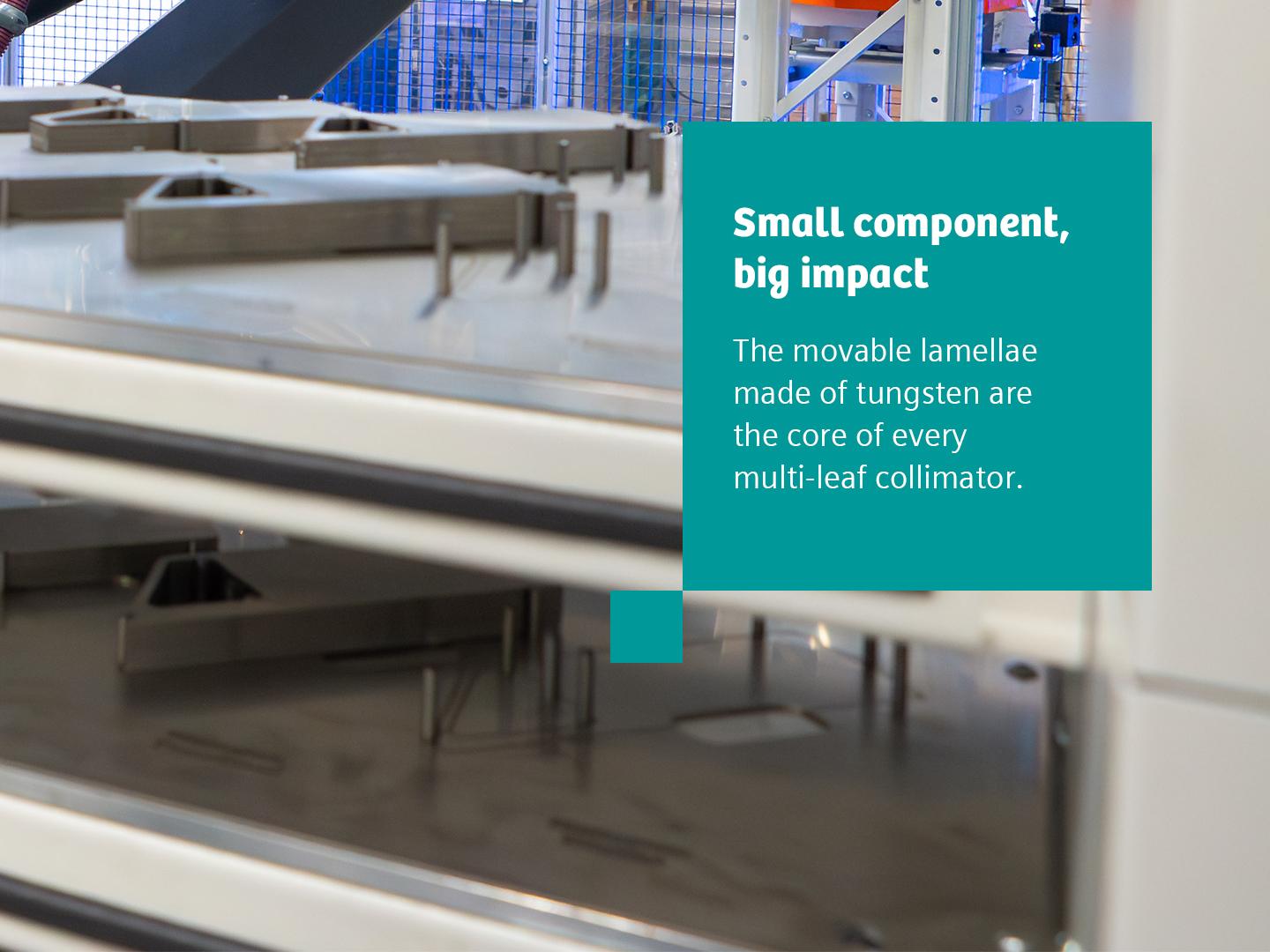
Turning precision into routine
Since February 2025, the Kemnath team has been manufacturing these vital components on a new, fully automated and digitized manufacturing line – delivering consistently high quality at three times the previous output.One of the toughest challenges was figuring out how to securely hold clamp the tungsten parts throughout the fully automated manufacturing and handling process. It took a smart, custom-engineered solution – developed entirely in-house – to make it work. “Our solution was key,” says Mayer. “It’s what made the entire automated processing of tungsten leafs possible.”
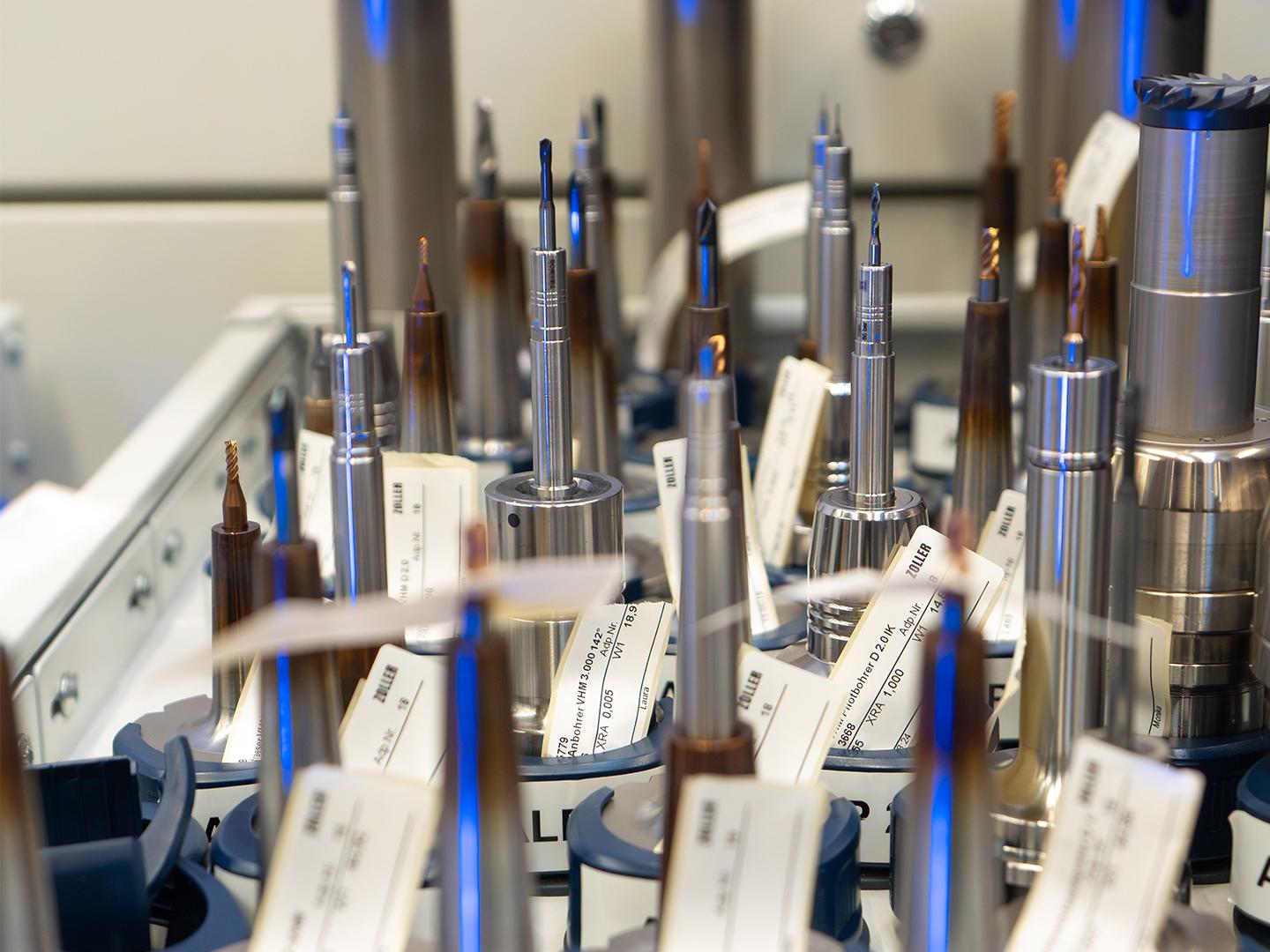
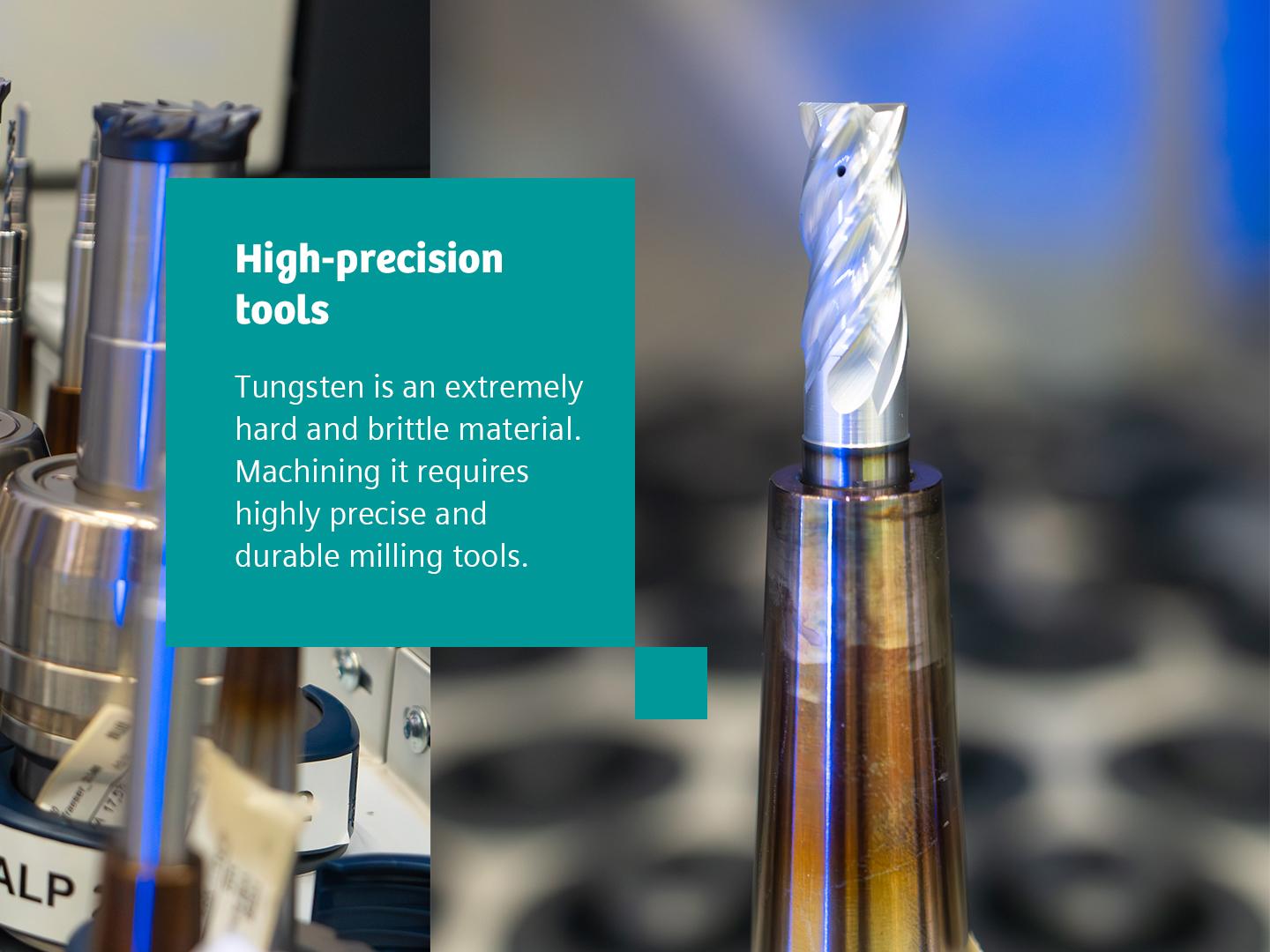
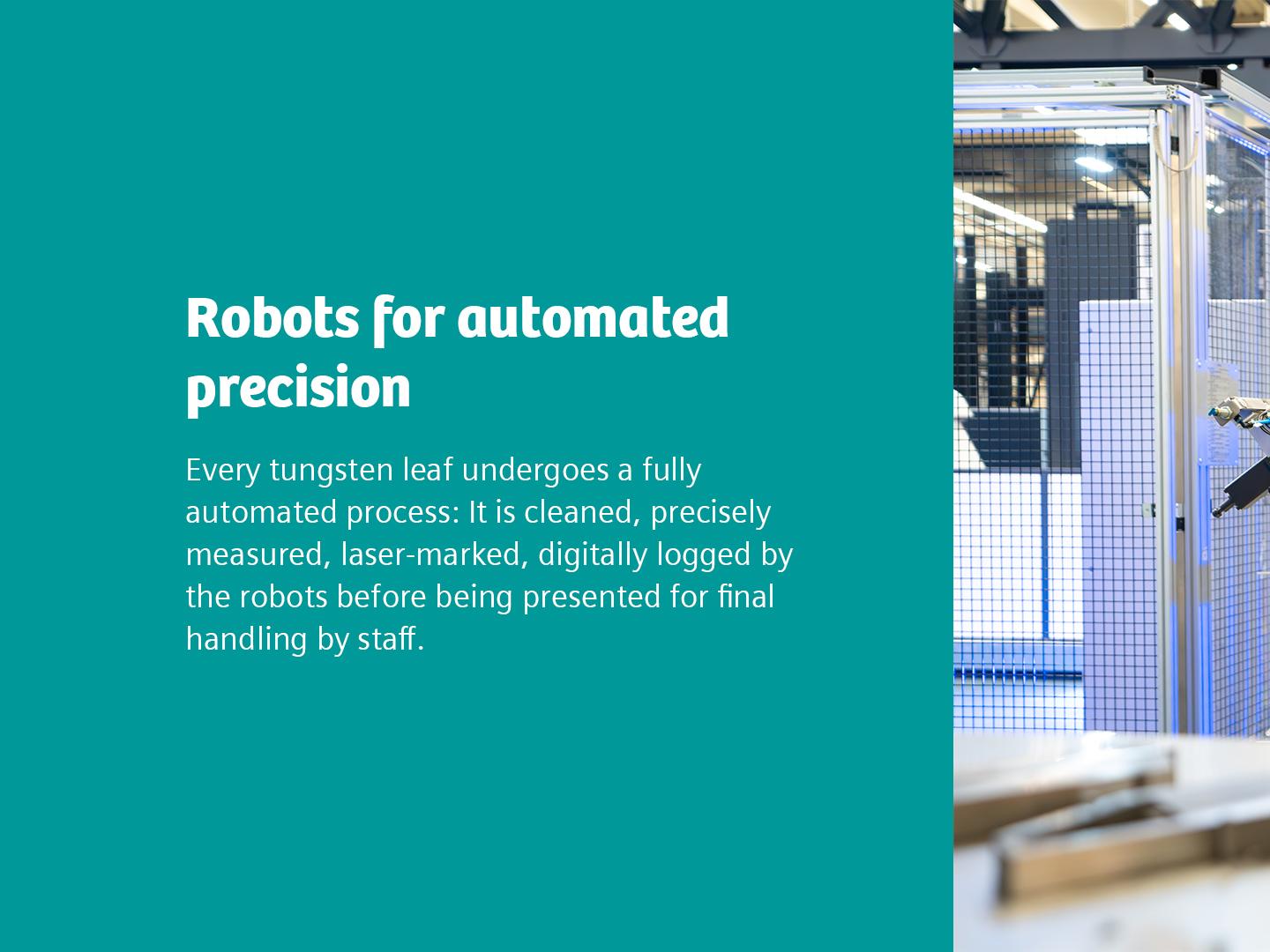
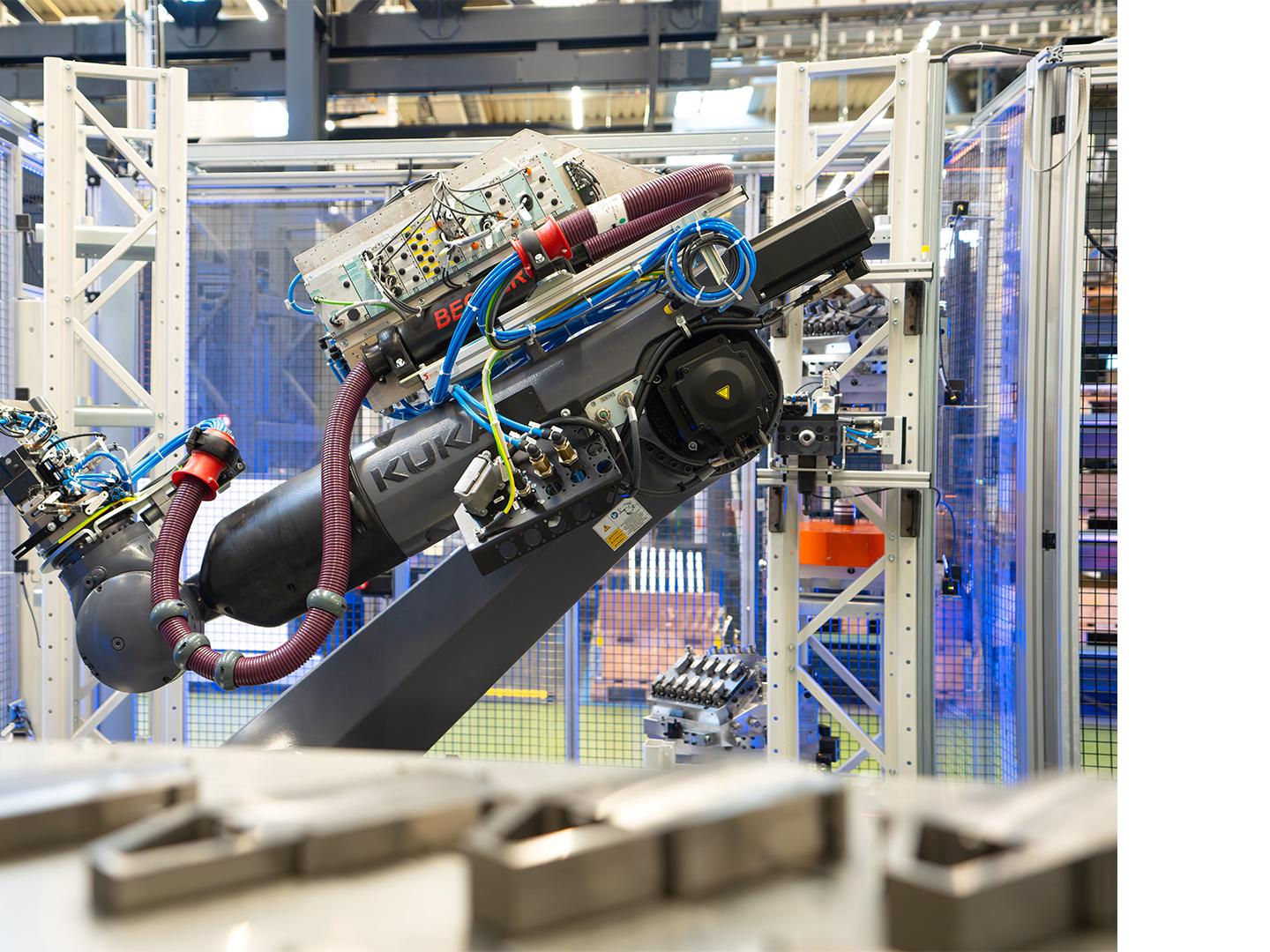
This automation increases the site’s manufacturing depth. That means we control most of the process ourselves – and that gives us independence from external suppliers, more reliable delivery to our partners, and long-term planning security. And all that at a time when global demand for high-precision collimators is on the rise.
Rainer Häupl, Head of the Kemnath Mechanical Center